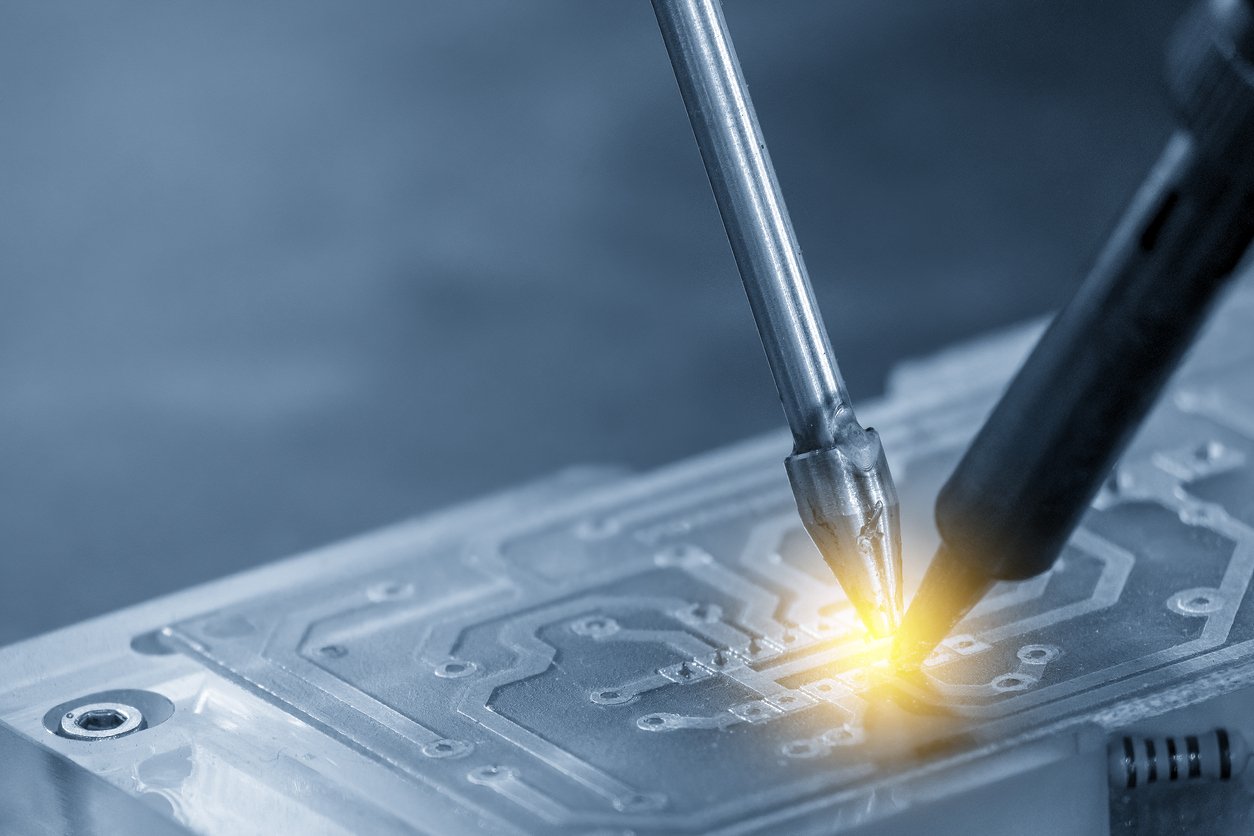
How Laser Welding Benefits the Electronics Industry
The speed and automation potential of laser welding helps manufacturers reduce production times and costs, making it an attractive solution for industries that need technology capable of welding two materials using a focused laser beam, mostly metals. In previous blogs, we talked about the use of laser welding in sectors where the welds require a low heat input to avoid damaging sensitive materials, like those used in the medical or automotive fields. This blog discusses the differences and benefits of laser welding in electronics.
One of the biggest advantages laser welding has for electronics manufacturing is that it can create welds that are incredibly precise, a necessary attribute due to the small and intricate components present in electronic devices. Secondly, the process is very fast, thereby allowing specifications to be achieved at higher speeds without negatively affecting quality. An important consideration when working with fragile or complex assemblies, the lack of physical touch in laser welding means there is far less risk of contaminating or damaging sensitive parts. Its utility is equally notable, capable of bonding to a wide range of materials that even include dissimilar metal and some plastics. Laser welding results in substantially lower thermal distortion thanks to its precision and direct control which, in turn, reduce requirements for post-processes and help improve overall quality of the product.
Laser welding is popular for its use in the manufacture of microelectronics, such as those that are to be soldered onto microchips, circuit boards, and sensors, resulting in stable connections even with delicate parts. For example, laser welding makes possible the connection of battery tabs, connectors, and housings during battery production with a level of accuracy required for high-performance battery use on devices such as smartphones and electric vehicles.
Laser welding is also key to optoelectronics—essential for applications ranging from LEDs to fiber optics, which require precise alignment and low thermal input to ensure maximum performance. These applications highlight the versatility and importance of laser welding to optimize capabilities and quality in modern electronic devices.
Following regulatory and quality standards is of utmost importance to guarantee safety and reliability when manufacturing electronics. This includes tough guidelines for manufacturing processes, material choices, and quality prospects applied to manufacturing electronic circuit boards: ISO 9001IPC for electronic assemblies. The advantages of laser welding quality are extremely important in these target areas, delivering accuracy and consistent reliability typical for all laser processing.
Laser technology offers so many advantages that each industry segment has its own unique selling proposition. Amglo’s laser flash lamps have attained market leading positioning within all sectors and applications, from industrial welding, cutting, and marking to inspection tasks. All our products are developed with a prioritization on durability, performance enhancement, and lifespan to cater to a variety of unique applications.