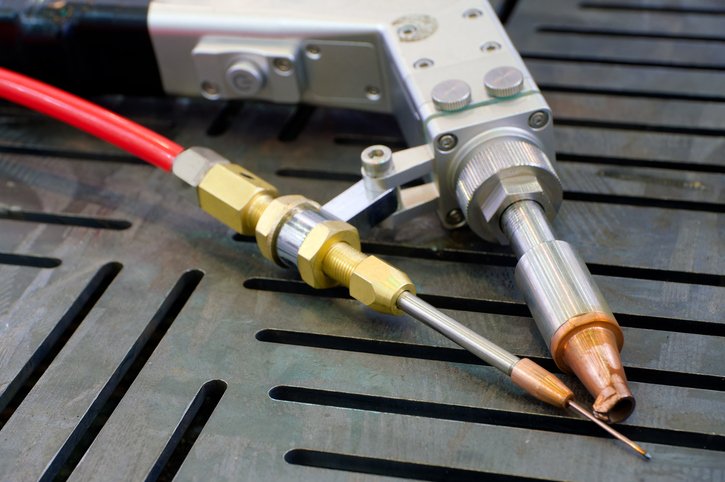
The Laser Welding Advantage in Tool and Die
Manufacturers in the tool and die industry know that precision is paramount. Laser welding delivers this precision with unmatched accuracy. Utilizing a concentrated beam of light, laser welding has the capability to achieve welds that are both fine and exact, accommodating the intricate details of the industry’s complex molds and die-cutting tools. This level of precision ensures that each product adheres strictly to specifications, resulting in minimal distortion and exceptional fit and finish. When utilizing laser welding in the process, the creation of detailed, high-quality components becomes seamless.
Delivering speed, efficiency, and sustainability
In addition to precision, the efficiency gained from laser welding technology makes it possible for manufacturing facilities to respond swiftly to market demands. The ability to enable rapid and automated welding processes drastically cuts down manufacturing and assembly times, minimizes setup times, and facilitates continuous operation. All this not only optimizes production, it also ensures timely delivery without sacrificing quality.
Laser welding also offers a significant advantage in reducing material waste. The exceptional precision of the laser means that only the exact amount of material needed is used, eliminating excess and minimizing scrap. Additionally, the inherent accuracy of laser welding reduces the need for extensive post-weld processing, which subsequently cuts down on labor and material costs. By minimizing the need for additional finishing work, manufacturers can streamline their production lines, resulting in faster turnaround times and lower operational expenses.
The efficiency that laser welding delivers is yet another way companies can support corporate goals for environmental sustainability. As the industry moves towards more sustainable practices, the energy efficiency of laser welding systems will be further optimized, contributing to greener manufacturing processes. When transitioning to laser welding technology, manufacturers can produce high-quality products at a cost-effective advantage, as well as boast an eco-friendly operation.
With the ability to create intricate designs and sharp edges, laser cutting and welding provide high levels of accuracy that are difficult to achieve with traditional methods. Additionally, laser technology offers flexibility in working with various metals and alloys, making it suitable for complex and customized projects. The non-contact nature of lasers also minimizes wear and tear on tools, leading to longer tool life and reduced maintenance costs.
Innovations and future trends
Laser welding has been called a game-changer for tool and die manufacturers, but it requires understanding the process to unlock its full potential. Leveraging an understanding of laser welding’s capabilities makes it easier to troubleshoot issues before they escalate, ensuring that every weld meets stringent industry standards. This proactive approach can further minimize downtime and enhance overall productivity, enabling manufacturers to maintain a steady workflow.
Looking ahead, laser welding is poised to integrate more sophisticated technologies, such as AI, further elevating its impact on the tool and die industry. Additionally, new materials and alloys explicitly designed for laser welding are expected to emerge, broadening the range of applications and improving the durability of welded joints. With continuous innovation in the field, it is important to stay informed about emerging technologies and integrate them into new capabilities.
Amglo supports the laser market with highly engineered lamps that are used by many leading manufacturers due to their high performance. We have developed a range of products precisely manufactured to meet specific light output and color rendering requirements, providing consistent and reliable lighting without interruption. The choice of leading OEMs, Amglo’s lamps focus on high reliability, optimum performance, and long lifetime.