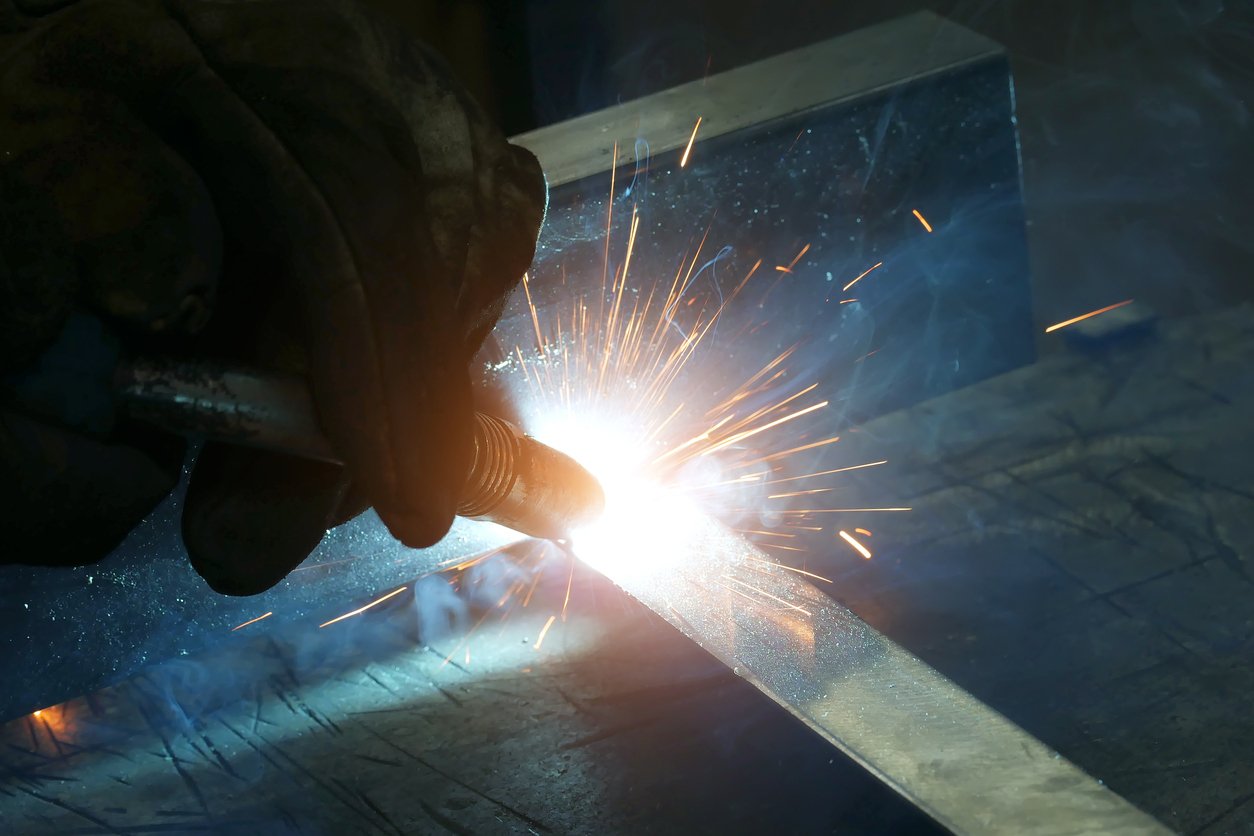
Laser Welding Delivers a Flexible Production Process for Automotive Manufacturers
Today, lasers are widely used in manufacturing for the ability to achieve precise cutting, welding, and engraving, as well as high accuracy and speed. They enable intricate designs and shapes in materials like metals, plastics, and ceramics, making them essential for producing everything from automotive components to electronics.
The speed and automation potential of laser welding helps manufacturers reduce production times and costs, making it an attractive solution for automotive manufacturing plants. While laser welding is helping manufacturers in the automotive industry achieve higher quality, efficiency, and flexibility, there are two additional benefits to consider: safety and the environment. Laser welding systems can be enclosed and automated, reducing exposure to hazardous fumes and improving worker safety. The process produces less smoke and spatter than traditional welding, creating a cleaner working environment.
Additionally, as the demand for lighter, more fuel-efficient vehicles grows, manufacturers need advanced techniques that allow for stronger, yet lighter, welds. Laser welding provides a high level of control, enabling the joining of various materials with minimal heat distortion, which is crucial for maintaining the integrity of lightweight alloys and advanced composites. Hence, laser welding is now in demand when handling complex assemblies made from various materials, including body frames, door frames, trunks, auto hoods, front and back lights, and electronic housings.
For example, two major high-end manufacturers use laser welding extensively in the body-in-white stage, where the car’s body is assembled from sheet metal components. Laser welding is used for joining roof panels, side frames, and door structures. The precision of laser welding ensures strong, clean joints with minimal heat distortion, which is crucial for maintaining the dimensional accuracy of the car’s structure.
Electronic vehicle manufacturers also use laser welding to assemble battery enclosures. The process is ideal for sealing the aluminum or stainless-steel enclosures that house the batteries, providing a strong, hermetic seal that protects the battery cells from environmental factors. The precision of laser welding also reduces the risk of damaging sensitive battery components.
Laser welding offers numerous advantages in the automotive industry, making it a highly efficient and effective manufacturing process. One of its primary benefits is precision, allowing for exact and consistent welds, which enhances the structural integrity and performance of vehicles. The process is also faster than traditional welding methods, increasing production speed while reducing labor costs. Overall, laser welding contributes to higher-quality, lightweight vehicles with improved fuel efficiency and safety.
Amglo supports the automotive laser market with highly engineered lamps that are used by many of the leading automotive manufacturers due to their high performance. We have developed a range of products precisely manufactured to meet specific light output and color rendering requirements, providing consistent and reliable lighting without interruption. The choice of leading OEMs, Amglo’s lamps are recognized for their high reliability, optimum performance, and long lifetime.