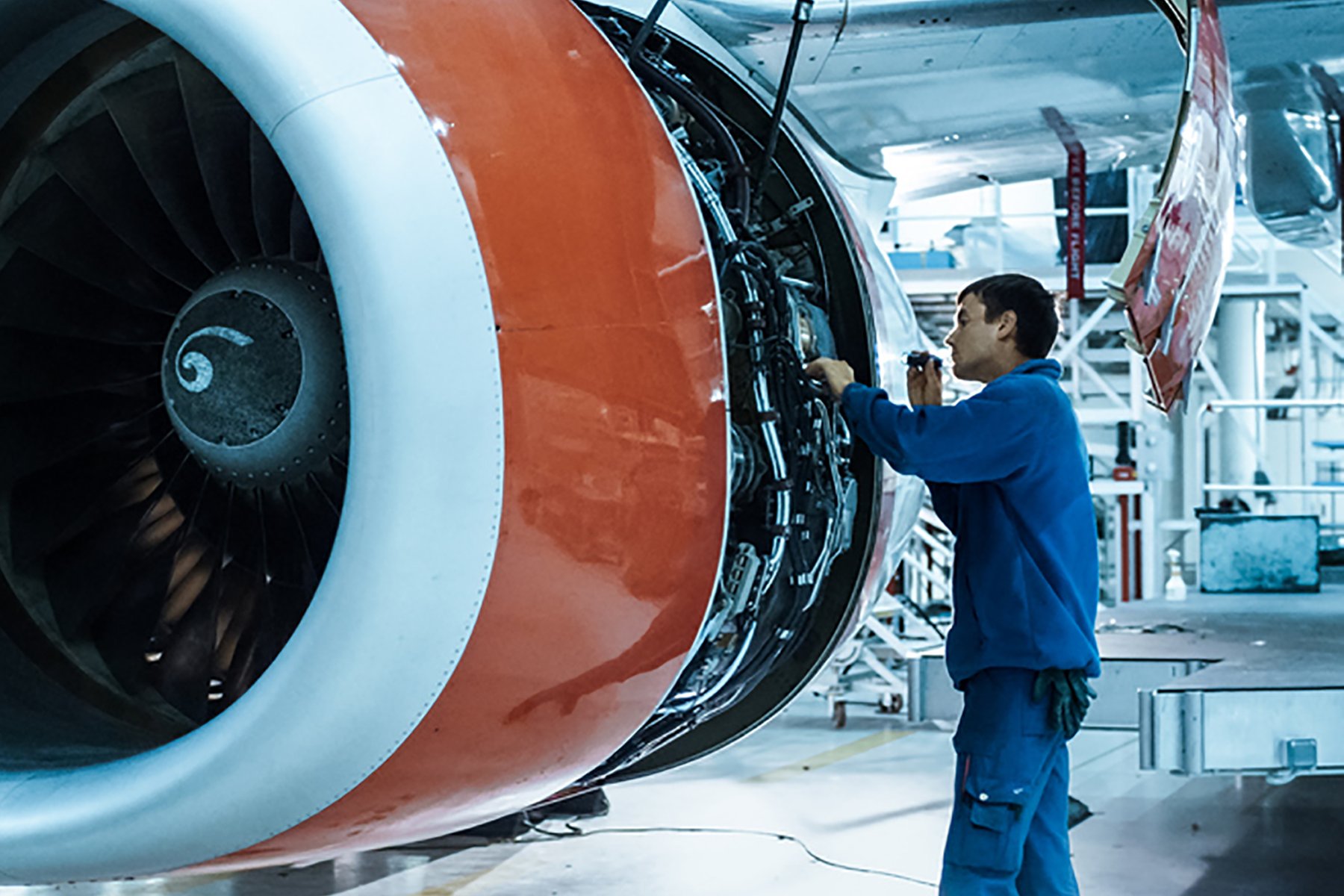
How Laser Welding is Transforming Aerospace Manufacturing
Laser welding stands as an emerging force within the aerospace industry, touching a wide array of applications from the assembly of airframes to the functionality of security metal detectors. Recognized for its exceptional precision and unparalleled strength, this cutting-edge welding technology is redefining the way aerospace components are designed, fabricated, and maintained. A significant part of its appeal lies in its capacity to deliver highly accurate joining solutions that align with the stringent safety, reliability, and performance benchmarks of this demanding sector.
One of the greatest advantages laser welding brings to the aerospace manufacturing arena is the achievement of superior weld quality with minimal imperfections. This is especially crucial for meeting the exacting safety and performance standards necessary in aerospace contexts. The high precision inherent in laser welding allows for the flawless joining of intricate components and complex geometries—tasks that often pose significant challenges to traditional welding methodologies.
Moreover, laser welding is not only precise but also a remarkably swift and efficient process. This efficiency translates to shorter production times and lower overall manufacturing costs. The minimal heat input characteristic of laser welding helps maintain the structural integrity of delicate materials, reducing thermal distortion and thereby extending the lifespan of aerospace components.
Despite the traditionally slow adoption of new processes within the aerospace industry due to stringent qualification protocols, laser welding presents manufacturers with several advantages that have a direct impact on the performance, safety, and efficiency of aircraft and spacecraft.
These include:
• Weight Optimization: In aerospace design, reducing weight is paramount for enhancing fuel efficiency and overall performance. Laser welding enables the use of thinner and lighter materials without sacrificing joint strength. This leads to lighter airframes and components, which in turn boost fuel efficiency and lower operating costs.
• Simplified Assembly Processes: Integrating laser welding into the design phase allows aerospace engineers to cut down on the number of mechanical fasteners, rivets, or other traditional joining methods. This streamlines the assembly process, reducing the total number of parts needed and resulting in more efficient production and maintenance cycles.
• Structural Integrity and Reliability: Laser welding produces strong, high-quality welds with minimal porosity and defects, ensuring the long-term reliability of critical components. This fortifies the overall structural integrity of aircraft, enabling them to withstand extreme conditions such as elevated temperatures, pressure, and vibrations.
• Material Versatility: Aerospace components are frequently composed of advanced materials like titanium, nickel alloys, and aluminum, which are notoriously difficult to weld using conventional methods. Laser welding excels at quickly joining these materials, ensuring robust and reliable joints with minimal defects.
• Compliance with Regulatory Standards: Aerospace components must adhere to strict regulatory requirements. Laser welding offers the high quality and reliability necessary to meet the certification standards set by aviation authorities.
Amglo’s laser flash lamps are extensively utilized across the aerospace industry, where continuous, round-the-clock operations demand the highest-quality light sources for numerous applications including welding, cutting, laser marking, and inspection. By prioritizing reliability, optimal performance, and extended lifetime, Amglo continues to produce a diverse range of products for industrial laser markets that emphasize efficiency, productivity, and overall cost-effectiveness.