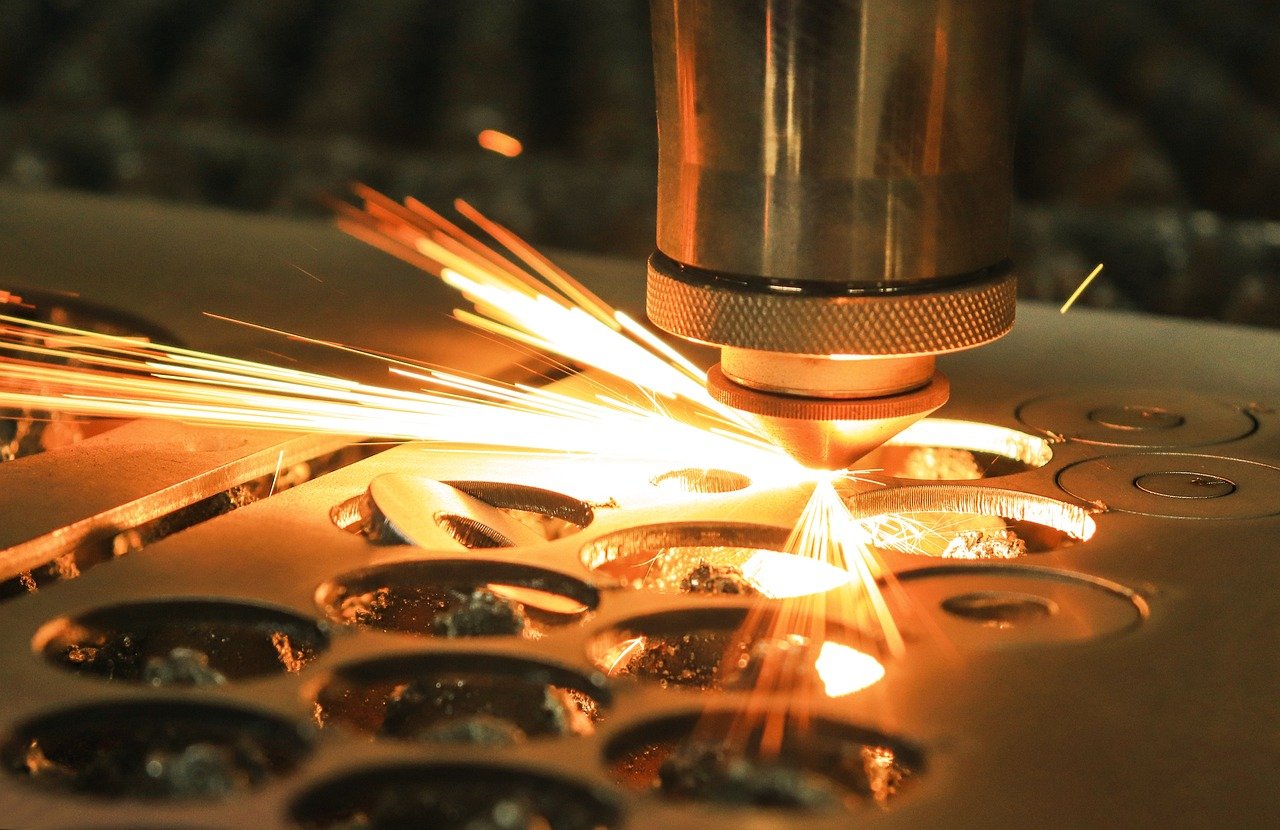
3 Ways Industrial Flashlamps Support Today’s High-tech Manufacturing
What’s behind the creation of the technologies that are necessary for modern living? Think about the precision required to make components like semiconductors in your smart phone, engine parts and sensors in your electric vehicle, and all the thousands of parts that make up a modern jet engine, helping you travel for business or pleasure anywhere. Whether it’s cleanly cutting metal with laser, welding with laser, or marking with laser, flashlamps are behind the power of these manufacturing tools.
The market for the usage of laser in industry and manufacturing is growing. For instance, according to recent market research, demand for laser welding equipment is projected to hit a compound annual growth rate of 5.7%, with the automotive industry contributing to this growth.
Here are three examples of how flashlamps for laser systems support manufacturing for a high-tech world, with insights from the American Society of Mechanical Engineers (ASME):
1. Laser cutting: Xenon flashlamps can be used for non-contact laser cutting, resulting in high quality dimensionally accurate cuts. The benefits of laser cutting compared to mechanical cutting include a higher level of precision and faster production speeds. Laser cutting can be applied with several types of metals and polymers. Examples of materials that can be cut include aluminum, titanium, and steel, with micron-level tolerances.
2. Laser welding: Xenon flashlamps provide laser welds formed as the intense laser light rapidly heats the material. Laser welding is particularly effective for welding materials with complex geometries or dissimilar materials that are more complicated to join together, such as metals and plastics. This type of welding is also excellent when high precision is required for very small welds.
3. Laser marking: Xenon flashlamps are used as a method to mark materials using a fine spot diameter to enable tracking and traceability across many industries. Laser marking is being used more often in imprinting unique identification (UID) numbers on parts and products so they can be traced back if a recall occurs. The markings include human-readable and barcode information. For medical devices, these marks can withstand many cycles of sterilization.